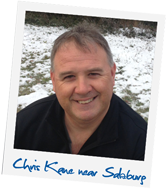
IN PARTNERSHIP
Foreign correspondent and Productivity Partnership Manager Chris Kane filed this report "on the road" during his recent study tour of prefabricated building technology in Southern Germany and Austria. The tour was led by Johann Betz, a German engineer with considerable experience in factory-based "industrialised" construction who now lives in Christchurch.
The tour is fascinating, from the wider perspective of the New Zealand construction industry. Just after the Second World War, Germany was faced with unaffordable housing in short supply and of low quality. In response, part of the construction sector consciously chose to "rationalise" how they built; basically, to question each decision made and each step of the production process.
The result has been that about 15% of the 100,000 houses built each year in Germany are prefabricated to a very high degree.
The tour has had a strong (but not exclusive) timber focus, which is entirely appropriate as Central Europe has a long history of timber construction. We've visited a number of factories where walls, floors and ceilings – basically anything that can be made into panels – are made from timber elements.
The difference from New Zealand in construction techniques is very noticeable. In Germany massive use of timber is common. Walls around 300mm thick are the norm, primarily because of the need to insulate to a very high degree. Most of the buildings we have been in – show homes, shops, hotels, even factories – are triple-glazed (and with the temperature outside currently at about minus five degrees, they need to be).
Main findings
There have been two main findings from the trip:
1. |
Sustainability, energy and carbon footprints drive a lot of behaviour in Central Europe. The use of wood is seen as being sensitive to those issues. In fact, it appears that the more wood used, the better the house is perceived to be! This is an interesting contrast to our approach of engineering out every last unnecessary millimetre on cost grounds. |
2. |
The prefabrication industry organised itself in the 1960s to document and achieve much higher construction and performance standards than the site-built competition. Over the years since, standards have increased in stringency, and new ones have been introduced, to the point where prefabricated houses now command a price premium over site-built houses. |
Transferring learnings
The most obvious question is "could German prefabrication techniques be transplanted to New Zealand?" The answer is very probably no, primarily because the ecosystem that supports the delivery of prefabricated buildings in Germany is not present in New Zealand.
Could we develop our own systems (tailored to the New Zealand market and climate) and deliver them in a similar manner to those in Germany and Austria? Yes, undoubtedly, given enough time. Given the pressures of housing affordability and supply (see the Partnership's National Construction Pipeline report) it's obvious that New Zealanders wanting to take up prefabrication and industrialised construction won't have 60 years to grow the supporting ecosystem.
So the next question is: "what can we do in TEN years?"
The Partnership will be working with PrefabNZ to help create wider awareness of their work. We will also be working inside the Ministry of Business, Innovation and Employment to identify and remove unnecessary barriers to wider uptake of prefabrication and industrialised construction in New Zealand.
My final thoughts are that we have the insight to where the techniques seen in Germany could be applied and we know that there is considerable and enduring construction demand so there may never be a better time to adopt new ways of building.
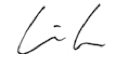
Chris Kane
Back to top
|