ANOTHER LOOK AT PREFABRICATION
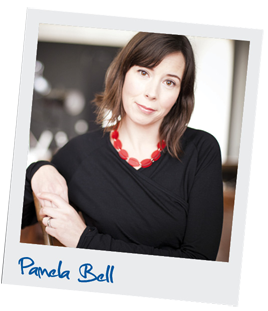
Late last year PrefabNZ Chief Executive Pamela Bell joined Productivity Partnership Manager Chris Kane and other key industry players to study use of prefabrication in construction in Germany and Austria. Chris shared his tour highlights in our December newsletter. Pamela continues the conversation with her observations.
"Imagine a supermarket for houses…an outdoor store with 60 or 80 different houses to choose from. First you choose the design you like and then make the detailed choices such as roofing and cladding, all in the same place." Showhome village Bauzentrum Poing is one of Pamela's outstanding memories of the study tour. She says that providing a sophisticated front door to the industry is something we can learn from immensely. "PrefabNZ is replicating that in a very small scale with our Hive Home Innovation Village in Christchurch. The idea is that customers can touch and feel everything. Germans are great at making the home build process customer focused. Everything is presented in a client friendly way, right down to play areas for children.
Need for transparent demand
Pamela recognises that the size of our market presents a challenge. "The main barrier to more prefabrication in housing construction is the need for transparent demand – a sizeable pipeline of work in one place - so that businesses can justify investing in the required machinery. What we saw is achievable in New Zealand but the technology and systems would require much greater certainty of demand to be picked up and applied here."
In Germany use of prefabrication isn't just the domain of big players – a lot of small scale, third
generation businesses (like Keith Hay Homes and Lockwood in New Zealand) are "into it".
Panellised system pluses
"What's interesting is that small operators there design and build in one place," says Pamela. "It's an integrated construction process where logs go in one end and come out as a panellised housing system, ready to be assembled. It's not too far removed from what builders here already do. Pre-nailed roof trusses and wall frames are now standard. Prefabricated panelling is adding another product to the mix. Panels need to be assembled on site and internal finishing needs to occur but that gives builders a watertight envelope to work within."
Pamela says one of the positive spin-offs is a lack of weathertightness issues. "The builders we spoke to in Germany didn't know what we were talking about because water ingress doesn't happen to panellised systems made offsite and installed at site." Benefits include shorter build times, reduced risk and liability and increased client value.
Sustainability valued
Huge value is placed on future-proofing homes and making them sustainable so that running costs and long-term value are considered alongside the initial
cost of building.
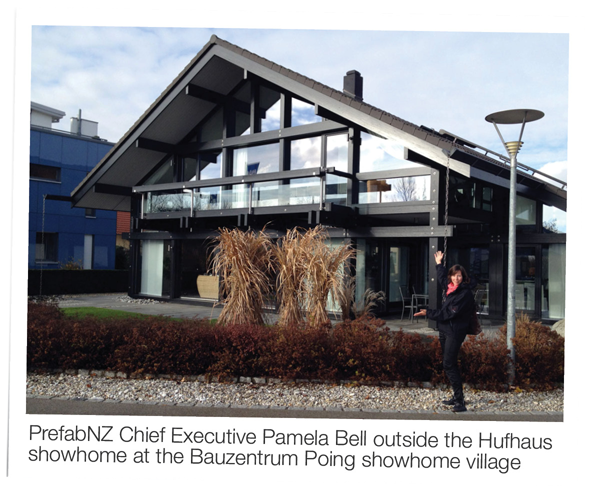
"We need to educate clients so they understand cost in different dimensions and communicate value to the next purchaser. Things like double glazing, insulation in walls, solar heating and low maintenance finishes provide a return on investment over time. It's about creating a quality environment in which to live."
Pamela believes the need to take a lifecycle view of value is applicable across the industry.
"Volume builders need to pay particular attention to future-proofing. If New Zealand companies don't take up further prefabrication and higher quality construction methods, they are open to being undercut by competitors from China and Australia."
Lack of variety isn't an issue with panellised prefabrication according to Pamela. "These places don't look like log cabins. Timber panels mostly have plaster finishes on the outside so they fit into traditional masonry construction. We're talking about a wide range of very sophisticated styles – like the Hufhaus on Grand Designs."
Enthusiastic about the possibilities, Pamela would like to see greater acceptance of prefabrication by both the industry and clients as a way of addressing housing affordability.
Learn more about the benefits of prefabrication at the PrefabNZ 2014 Conference, 26-28 March in Auckland.
Back to top
|