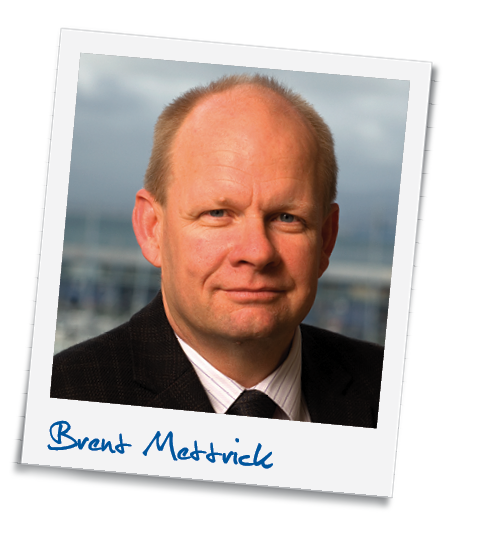
VALUE BUILDER - BRENT METTRICK
FOUNDER AND MANAGING DIRECTOR OF STONEWOOD
HOMES – ONE OF NEW ZEALAND’S LARGEST VOLUME
BUILDERS – FOUNDING MEMBER OF THE PRODUCTIVITY
PARTNERSHIP’S GOVERNANCE GROUP AND NATIONAL
PAST PRESIDENT OF THE REGISTERED MASTER
BUILDERS FEDERATION.
Brent Mettrick is a man on a mission, fixed on making a difference in two key areas:
1. |
The boom and bust cycle he believes cripples our construction industry. |
2. |
Housing affordability. |
Based in Christchurch, Brent travels the world to keep on top of construction innovation. In the last 12 months he has been to BAU, Munich – the world’s leading trade fair for architecture, materials and systems – the NAHB International Builders Show in Las Vegas and Ecobuild in the UK. He’s also fitted in a one-day “lean construction” seminar in the USA.
Here he shares his observations for the wider benefit of the sector.
|
For me, being part of the Partnership is about improving productivity and seeing if we can make the construction industry a better place. That means doing something to try and even out the boom and bust cycle.
Over thirty years in the industry I’ve seen a lot of people go broke when the market dips. Businesses ride high then go into survival mode. The impact of the sector’s volatility hits home when you have to let good people go – then they are lost to the industry.
An example of the cost to the industry is when I was forced to shelve a $400,000 software project in the middle of a downward spiral.
About three years ago being in this industry was like swimming in a river of rocks, rapids and piranhas. The market has improved but we need to turn the river into a beach people want to stay on.
We need to create an environment where the industry is seen as an asset, not a liability. The construction sector creates a lot of jobs and injects a lot of money into New Zealand’s economy – according to a PWC Report, $3 of economic activity is generated for $1 spent on construction. These efforts are often overlooked by economists and the Reserve Bank.
We can build the value of our industry by:
• |
Taking the complexity out of our build |
• |
Increasing the speed of our build |
• |
Building better for less cost. |
The Productivity Partnership is helping by identifying what levers are needed and where investment is required. It’s an effective forum to drive change, bringing together different parts of the industry. For once, the industry is looking to invest in itself for the good of the industry, rather than the good of individual suppliers.
Housing affordability
The other big concern for me is housing affordability. Affordability is about people getting into a home. The very first house I built was in Auckland and I sold it for $28,000 to a couple who were earning $171 per week with mortgage repayments of $67 per week. They thought that was steep. When I look at the numbers now, those people were very well off. We need to get back to the days where a home cost four to five times the average annual salary and we’re a long way from that.
Thinking like a manufacturer
Apart from land and finance, I believe the key barriers to housing affordability in New Zealand are:
• |
Compliance costs, including the high entry level to the market for international products |
• |
Fragmentation of our build process |
• |
Kiwi attachment to bespoke “customised” homes. |
These can be addressed by:
• |
Simplification (of regulation and the building process) |
• |
Standardisation (prefabrication, mass assembly) |
• |
Multiplication (volume building). |
We need to move to a manufacturing approach for new housing in New Zealand to make houses more affordable. The benefits of standardisation and multiplication haven’t been allowed to flow into the cost of a home to the level they should do.
Housing affordability is a numbers game. It’s about the cost of overheads per house and bricks and sticks per house. If you double your throughput you can halve your overheads, taking up to $20,000 off the cost of a home.
The cost of a house is mainly its external structure. Prefabrication and pre-assembly enable you to build more houses, faster. If you simplify the building process, you remove cost. In Germany a wall will arrive on site with cladding on and window in, with lining on, already gibbed and stopped. That wall will be installed and clipped onto another wall. It’s a very lean manufacturing process.
A workable solution
The Kiwi “norm” of building houses that are tailored to individual customers’ needs – bespoke homes – is highly inefficient and pushes up housing costs. A workable solution would be to segment New Zealand’s residential market into the volume/affordable market and boutique/premium priced bespoke market.
People forget about the end game – the focus has to be on Mr and Mrs Consumer who have to pay the mortgage and how much money they have to live on. We need to be open to new approaches to push the price of housing down. That frees up money in the rest of the economy.
Back to top
|