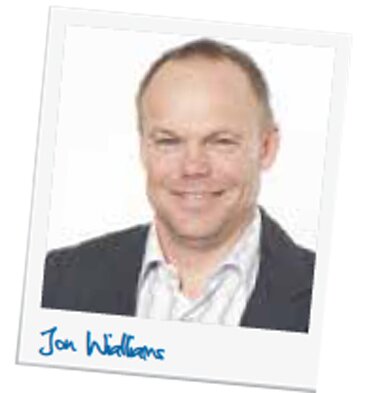
VALUE BUILDER - JON WILLIAMS
JON WILLIAMS IS A FAN OF BIM – WHEN IT'S USED WELL. AS BECA'S BUSINESS DIRECTOR-PRACTICE DEVELOPMENT HE'S FOCUSED ON ENSURING DESIGN PROCESSES AND TOOLS OPERATE AS EFFECTIVELY ACROSS THE BUSINESS AS POSSIBLE. HE WAS PREVIOUSLY GENERAL MANAGER OF BECA'S 200 BUILDING SERVICES ENGINEERS IN NEW ZEALAND. HIS EXPERIENCE INCLUDES 30 YEARS IN THE BUILDING SERVICES CONSULTING INDUSTRY IN NEW ZEALAND, THE UK AND AFRICA.
Jon has had a direct hand in the production of the New Zealand BIM Handbook, chairing the working group that put it together, and he is currently on the BIM Acceleration Committee. Here's his take on what BIM can really offer our construction industry.
"We want BIM" is something we're hearing increasingly as awareness of BIM grows. That's great but, like any tool, it's important that people know what BIM is and how to use it. I'd like to see a consistent understanding of BIM by the industry and make sure we don't invest a lot of time and effort in producing a lot of data that doesn't get used.
How to use BIM
In the New Zealand BIM Handbook we've defined 21 different use cases for BIM – things BIM can
give you. So all of the parties involved can get together at the start of a construction project and
discuss which of these they want.
"BIM is a lot more than a 3D drawing tool, it's the structured sharing of digital information in the built environment."
Using BIM intelligently means:
• designers know what they have to produce |
• contractors know what they're going to get |
• clients know what they are paying for. |
The most successful projects are those where builders and designers work closely together and BIM assists that. This includes more collaboration between designers including architects, services engineers and structural engineers who need to play better in the sandpit together!
What BIM is
BIM is a lot more that a 3D drawing tool, it's the structured sharing of digital information in the built environment.
3D modelling has been around for some time but you can use BIM to create data for many purposes and use it many times. The key difference between BIM and 3D CAD is that in a BIM development tool you don't just draw lines and dots, you draw a pipe or wall with real life attributes, eg, 100 mm thick with 9 mm plasterboard either side, painted green. It's a very data rich model of a building which enables you to use the design to optimise construction. You can configure BIM to work out an area schedule, check height to boundary ratios, check there are the right number of toilets, check compliance with the building code, build in rules, eg, "for every 1000 metres of floor space you need 1.5 metres of stair width". It can help specifications for and costing of a job, eg, if I make that a little shorter I can save 1000 m2 of plasterboard or 100 tonnes of steel. You can interrogate the data.
Reaping the benefits
BIM can be applied to commercial and institutional developments – schools, airports and sky towers – as well as residential buildings. To some extent, the benefits are easier to realise for SMEs because there are fewer players to co-ordinate.
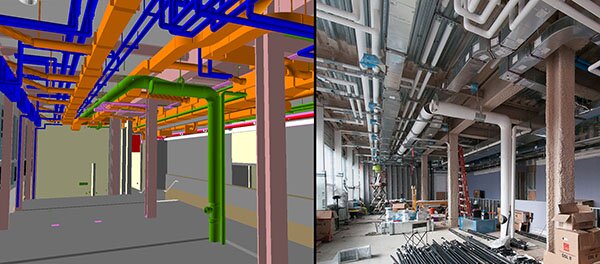
Image: Princeton University
BIM can offer you significant benefits but you need to make sure you're going to take advantage of those benefits before you invest in the cost. BIM's not something you need to buy – you can get a licence for a drawing tool for around $6000 – but use of the data is key; you need to know how to extract the information you want from it.
Beca has been using BIM in the industrial space for 10 to 12 years, for instance, linking modelled designs to maintenance systems. Increasingly, we're using BIM in the building space where it's being seen as "the new green" – an environmentally friendly tool. For the Middlemore Hospital project Beca handed over our BIM model to the constructor for direct input to the production of shop drawings. For an Auckland University project the information within the model is being given a labelling system that aligns with the University's asset management system. In Australia, Victoria's desalination plant was modelled in 3D to co-ordinate the design with the vendor equipment that needed to be installed in it, to ensure easy access to it for maintenance when in operation. On that project there were regular meetings with the project team where we linked our computer to big screen TVs and walked through the virtual construction, identifying clashes and clearances.
BIM highlights problems more clearly than the conventional design process. It creates a greater level of co-ordination. Creating a 3D model allows people to visualise a space and to understand what they will get in practice in a virtual sense. It means you can build faster because everyone knows how things are going to fit together on site and that lowers cost. The end result is increased client satisfaction. But virtual co-ordination has a cost too, and you need to put limits on what you are asking BIM to do. The key thing is to decide if you are getting a benefit from it.
Back to top
|